Three Main Types of Warehouse Racking
The key to designing an efficient warehouse is setting up racking systems that optimises the available storage space, while making it easy for people and goods to move around. This usually requires a mix of different types of warehouse shelving. This guide describes the main types of warehouse racking systems, their benefits and their best applications.
While it may seem like there is an endless variety of racking, in a practical sense, there are 3 main racking systems that are relevant to setting up a warehouse:
-
Pallet racking that is designed for the handling of palletized goods with forklifts and mechanical picking platforms
-
Industrial Shelving that is designed on a human scale for manual picking and handling
-
Specialist racking that is designed for special applications and odd shaped items
Set out below is a brief description of the various shelving and racking types that fall within each of these three categories.
1. Pallet Racking Systems
Warehouse pallet racking is a type of shelving used for holding palletized goods. Palletizing goods is useful, as it makes handling, put away and picking so much easier.
It's possible to store loaded pallets directly on the floor, either singly, one pallet high (floor stacking) or stacked one on top of another (block stacking). This is a useful storage method for some bulky items. However, a high quality pallet racking system is a more efficient and systematic use of the vertical space in a warehouse.
Pallet rack systems are one of the most common warehouse storage systems. Essentially, it is a very heavy duty storage system that stores pallets of goods in horizontal rows on multiple levels within a vertical, steel rack. The pallets are typically loaded onto the racks and unloaded with the aid of a forklift.
It is important to ensure that your pallet racking meets Australian Standards such as AS 4084:2023, which sets out the compliance requirements for the design, operation, and maintenance of steel storage racking.
There are 3 main types of racking for pallets:
- Selective Pallet Racking
- Drive-In & Drive Thru Pallet Racking
- Pallet Flow Racking
1.1 Selective Pallet Racking (static racking)
Selective pallet racking is so called, because you can “select” a pallet without having to move other pallets out of the way. Notably, it is the simplest and cheapest type of pallet racking and it works well with any type of forklift, without the need for specialized material handling equipment.
A static pallet racking system is most commonly 1 pallet deep (single deep). However, you can opt for a two pallet deep configuration (double deep), if you need to store multiple pallets.
1.1.1 Single Deep
Unless specified otherwise, a Selective Pallet Rack generally refers to single deep racking. Single deep selective racking is the most common type of warehouse racking for good reason. It is a very versatile warehouse storage solution; each pallet position can hold a different product or SKU. In addition, each pallet is easily visible and the configuration allows direct access for loading and unloading at any time. So damage during handling is less likely.
It is available in a range of heights and depths and is easy to install and dismantle. Changing the mix of products in the warehouse is simply a matter of swapping out pallets. So it is suitable for both fast and slow moving goods.
Selective pallet rack systems are easy to source and are inexpensive on a cost-per-pallet position basis. A standard forklift with tines is all that is required – no need for special attachments or lift trucks.
It is ideal in situations where there are a large number of different products with low volumes, and different weights and sizes that have a low turnover or are perishable. It is easily configured and works well in warehouse operations that use a First-In, First-Out (FIFO) inventory system. So it suits industries such as manufacturing, retail, food and beverage and pharmaceuticals.
On the downside, it doesn’t provide the same density of storage as other storage options and it requires numerous, wide aisles so that the forklifts can access and maneuver the pallets.
1.1.2 Double Deep Pallet Racking
Double deep or double reach racking shares the same components as single deep racking. The difference is that it’s twice as deep, so each position can accommodate two pallets, one in front of the other. This modification increases the storage capacity of the warehouse space, by reducing the necessary aisle space. However, it does require a special, “double reach” forklift to maneuver the pallets at the back of each position.
A double deep racking system suits situations where there are multiple pallets of the same product stored in-line, back-to-back and where the inventory is managed using a Last-In, First-Out (LIFO) system.
Double deep racking may cost a bit more to implement and may reduce the capacity to efficiently store a wide variety of products. However, the trade off is the increased storage capacity that it offers. It suits applications such as general warehousing and manufacturing, retail and food and beverage warehousing.
1.1.3 Modified Pallet Racking
Modified pallet racking is made from standard pallet racking components, plus some additional modified parts to accommodate odd-shaped (ugly) items. This type of racking is often combined with special material handling vehicles or forklift attachments. Some of the common, modified storage solutions are described in the table below.
Application |
Description |
Coil/ Drum Racking |
- Storage of steel coils and drums
- Uses pallet racking uprights and beams with the addition of steel cradles to stop stored coils and drums from rolling
- Forklift is mounted with a drum racker
|
Cable Racking |
- Storage of cable drums or spindles
- A steel rod is positioned through the centre of the drum to place on brackets attached to the racking uprights
- Forklift has a special attachment for placing/ removing cable drums and spindles
|
Carpet Racking |
- Storage of carpet and vinyl rolls
- Carpet racking is a deep racking system that allows for the storage of carpet rolls in a pigeon-hole style
- Forklift has a roll prong attachment
|
Sheet Racking |
- Storage of sheet materials like gyprock, sheet metal, wood and plastics
- Uses pallet racking uprights and beams to create the correct sized locations
- Forklift has standard tines
|
1.2 Drive-in and Drive-thru Pallet Racking
Drive-in/ Drive-thru racking is a high density storage system. It does away with the horizontal shelves of selective racking and replaces them with ledges on the uprights. The left and right side of each pallet is supported on these ledges and the middle of the pallet is suspended in the air. In this way, the space between the uprights is open, creating a lane that standard-tine forklifts can drive down to deposit a pallet at different heights and depths on the available ledges.
The main advantage of this racking system is that it reduces the aisle space needed for storing stock and so significantly increases the storage capacity of the warehouse over a standard selective racking system.
For best effect, each lane should have low-medium turnover pallets that hold the same SKU’s. Thus it suits situations where there are many pallets of the same product.
These pallet racks come in two variations: drive-in and drive-thru.
1.2.1 Drive-In Racking
Drive-in pallet racking has only one access point at the front. Pallets are loaded and retrieved by a forklift driving into a lane to place or pick up a pallet that is up to 4 spaces deep. The forklift then needs to back out of the lane to maneuver around the warehouse.
This system works best for Last-In, First-Out (LIFO) operations, where the last pallet loaded becomes the most accessible one and so the first one that is subsequently taken out. It suits environments where the inventory turnover isn't high and where the pallets are of uniform size and have relatively uniform loads. As a result, it doesn’t suit products that are perishable, have a short shelf life or are easily damaged.
1.2.2 Drive-Thru Racking
Drive-thru is essentially the same system as Drive-in racking except there is access from both the front and the back of each lane. Forklifts load the new pallets from the front and pick or unload the pallets they need from the back.
Because of the different loading and unloading positions, drive-through racking works best with First-In, First-Out (FIFO) storage operations, where many uniform pallets of the same product are stored together. For example: cold storage/ freezer rooms storing meat or flowers, beverage storage and chemical storage. It isn’t ideal for high turnover situations.
1.3 Pallet Flow Racking (gravity flow racking)
A pallet flow rack is a gravity-feed system, where the shelves slope down slightly from the back to the front. Rollers on the shelves allow pallets or cartons that are loaded at the back to roll forward under the effect of gravity. Items are then picked from the front. So it is ideal for a First-in, First-out (FIFO) system that involves perishable or seasonal items
1.3.1 Pallet Flow Racking
Pallet Flow Racking is a high-density, FIFO storage system, where a standard forklift loads pallets at the back of the racking and picks are unloaded from the front. It is the most expensive form of pallet racking, but it offers efficient high density storage.
The gravity feed system supports very high-density pallet storage of up to 20 pallets deep in one lane. This minimizes the number of aisles needed, while still maintaining efficient inventory turnover. The system enhances the put-away and retrieval process, so reducing the amount of labour required. As a result, it's great where there are limited numbers of high turnover SKU’s in large volumes and where those products have an expiry date.
Pallet flow racks are widely used in perishable-goods warehouses. It works well in freezer warehouses, food distribution centres and grocery warehouses.
Flow racking also comes in a form that works with cartons rather than pallets, which is called Carton Flow Racking.
a. Carton Flow Racking (Carton Live Storage)
It's possible to use the same gravity-fed strategy with smaller items, such as cartons and containers. Carton flow racks are designed specifically for small, non-palletized, lightweight items that require frequent and rapid picking.
Cartons are loaded at the back of the carton flow rack by hand and then unloaded manually from the front. Carton flow racking is sometimes used above a hand picking area as a buffer storage location that takes advantage of the available airspace.
1.3.2 Push-Back Pallet Racking
Push back racking is a similar gravity-fed system to pallet flow racking, except that the pallets are loaded and unloaded by standard-tine forklifts from the front only. The way it works is pallets are loaded onto an inclined track and cart system that slopes upwards as it goes back, 2-6 pallets deep. When an additional pallet is loaded, it pushes the previous pallet cart(s) upwards and to the back.
Thus the last pallet stored becomes the first in line for picking. So it suits LIFO based inventory systems.
One disadvantage of this system is that the pushing of the pallets creates a higher risk of damage.
Like the other gravity-fed storage systems, it suits the storage of numerous pallets of the same SKU. As a LIFO system, it works better with faster moving products that have a longer shelf life. So it is great for frozen products in cold storage rooms.
1.4 Pallet Racking Accessories
Importantly, you can improve the functionality, safety, and efficiency of your warehouse storage system by adding pallet racking accessories like those itemised below:
- Rack guards and frame protectors provide a shield against forklift damage in high traffic areas.
- Safety netting is often installed at the back of racks to help prevent items from falling and causing damage or personal injury.
- Dividers and wire decking help improve space utilization and accessibility. Dividers make it easy to separate different products within the same rack. While wire decking improves airflow, reduces dust buildup, and is required to meet fire code standards in many facilities.
- Clear labeling systems simplify inventory management by making it easy for workers to locate and pick items quickly.
2. Industrial Shelving
Industrial shelving is another type of warehouse racking. Specifically, it is medium to heavy duty shelving that is suitable for hand loading and picking (see example below). Sometimes it is used by itself in a warehouse installation, or for factory shelving. Alternatively, it is sometimes mixed with pallet racking to support different picking processes and so optimize the efficiency of a given industrial space.
The main types of industrial shelves are:
- Long span shelving
- Rivet shelving
- Wire shelving
- Mobile shelving
- Steel shelving
You can see a detailed explanation of the different types of Industrial Shelving in our separate blog post, here.
3. Specialist Types of Warehouse Racking
There are several specialist types of warehouse racking that are used for storing specific items, as described below.
3.1 Cantilever Racking
Cantilever racks are specifically designed for the storage of long, bulky and awkwardly shaped items. They consist of a series of vertical columns in a line that have horizontal arms on which the long items are stored.
There are two basic types of cantilever racking.
-
Single-Sided Cantilever Rack – has horizontal arms on the front side only, so you can position it against a wall
-
Double-Sided Cantilever Rack – has horizontal arms on both the front and back, so it requires access aisles on both sides
Cantilever racking makes lengthy materials easy to access. As a result, it is ideal for the storage of items like: lengths of timber, tubing, doors, steel, pipes, and furniture
3.2 Bulk Storage Racks
Bulk storage racks are constructed from robust materials to create a very high load bearing capacity. Specifically, they are designed to accommodate large and very heavy items that don't fit well on traditional shelving. As a result, they are often used for car engines and transmissions, machinery, and other oversized items.
3.3 Tyre Racking
Tyre racking is used to store rimless tyres in a vertical position to minimize warping and distortion (see image below). Tyres can be hand-picked by rolling them out when needed.
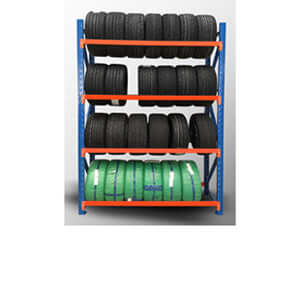
Falcon Shelving carries an extensive range of tyre racking and you can see the range here.
3.4 A-Frame Racking
A-Frame racking is designed in the shape of a capital letter "A". Long items are simply leaned against the slope of the A-Frame and stored vertically. Stored items are easy to access and the system maximizes the use of vertical space. As a result, it is great for long hand-picked items like lengths of timber and pipes.
3.5 Mezzanine floors
A mezzanine floor is a raised storage platform that is used to flexibly increase the available floor space. Sometimes the upper mezzanine level is used for extra shelving that is customized to the needs of the warehouse. At other times the mezzanine is used as: a workspace, a showroom for customers or as an office space.
4. Conclusion
Efficient warehouse storage design often relies on using a mixture of the different types of warehouse racking and shelving types to accommodate a range of stored items. So it is essential to understand the names, characteristics and benefits of the various racking systems, in order to make good decisions about the best way to layout a warehouse. Accordingly, this understanding is the first step towards good warehouse design.
If you are looking for longspan shelving you can contact our expert team to get more information on our products or an obligation free quotation. We can deliver to almost anywhere in Australia. Using our network of freight brokers and carriers we strive to get the best regular price and delivery options for each order.